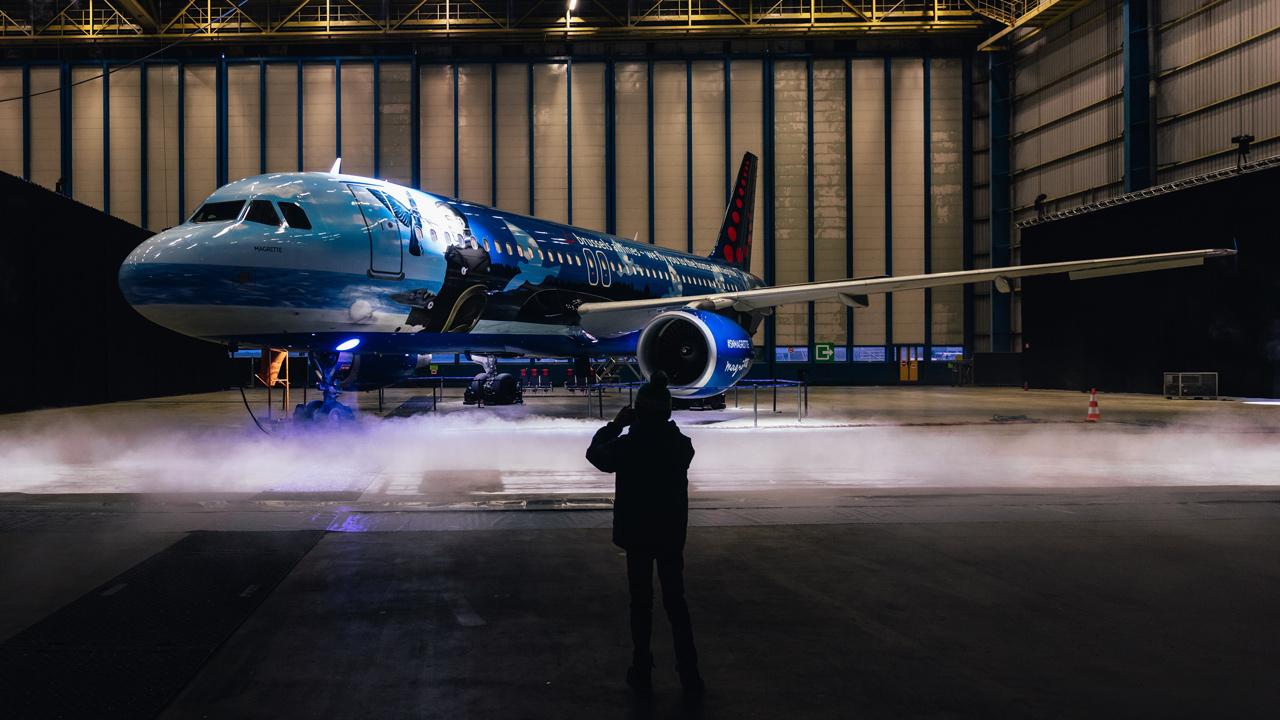
Megoldásokat nyújt majd a biztonsági szempontból kritikus termékek, így például a gépek, járművek, repülőgépek gyártásához és karbantartásához az Industrial Internet Consortium szervezet Track & Trace tesztprojektje. E szektorok közül számos egyre fejlettebb kéziszerszámokat használ. Annak érdekében, hogy jobban megértsük az intelligens kéziszerszámok jövőbeli felhasználását az iparban, elbeszélgettem Sébastien Boriával, az Airbus munkatársával. Sébastien az Airbus Factory of the Future (a jövő gyára) projektjének K&F mechatronikai műszaki vezetője.
– Sébastien, ön az Airbus vállalat Factory of the Future projektjén dolgozik. Ez egy igazán nagyratörő kezdeményezésnek hangzik. Milyen területek tartoznak e projekthez?
– Jelenleg több mint nyolcezer Airbus repülő üzemel szerte a világban, 2015. január 31-én összesen 15 276 légi jármű szerepelt a rendelési könyvünkben. Minden egyes repülőgép egy rendkívül összetett termék, amelynek több millió alkatrészét tökéletesen kell összeszerelni. Az innovatív gyártástechnológiák integrációja létfontosságú a termelékenység érdekében. Mára a digitális modelleket, a repülőgéptestre vetített lézereket és az összetett háromdimenziós környezeteket teljes mértékben integráltuk a folyamatainkba. Mivel minden gyártósor-generációnk élettartama az egy évtizedet is meghaladja, ezért a jövő gyárának tervezésekor egy évnél jóval távolabbra kell tekinteni. Számos fontos lehetőséget kell mérlegelni, ilyenek például az összeszerelést segítő robotizált külső vázak (exoskeleton), a fejlett robotok (a hagyományostól a kobotikáig /ember és gép együtt dolgozik/), az ALM-techológia (alkalmazáséletciklus-menedzsment), a globális tervezést segítő „virtuális fennsík” és az összeszerelő csarnok digitalizációja, az integrált gyártás és így tovább. A cél, hogy kihasználjuk az olyan újonnan megjelenő technológiákat, amelyeket adaptálhatunk vagy továbbfejleszthetünk a gyártásfolyamataink javítására.
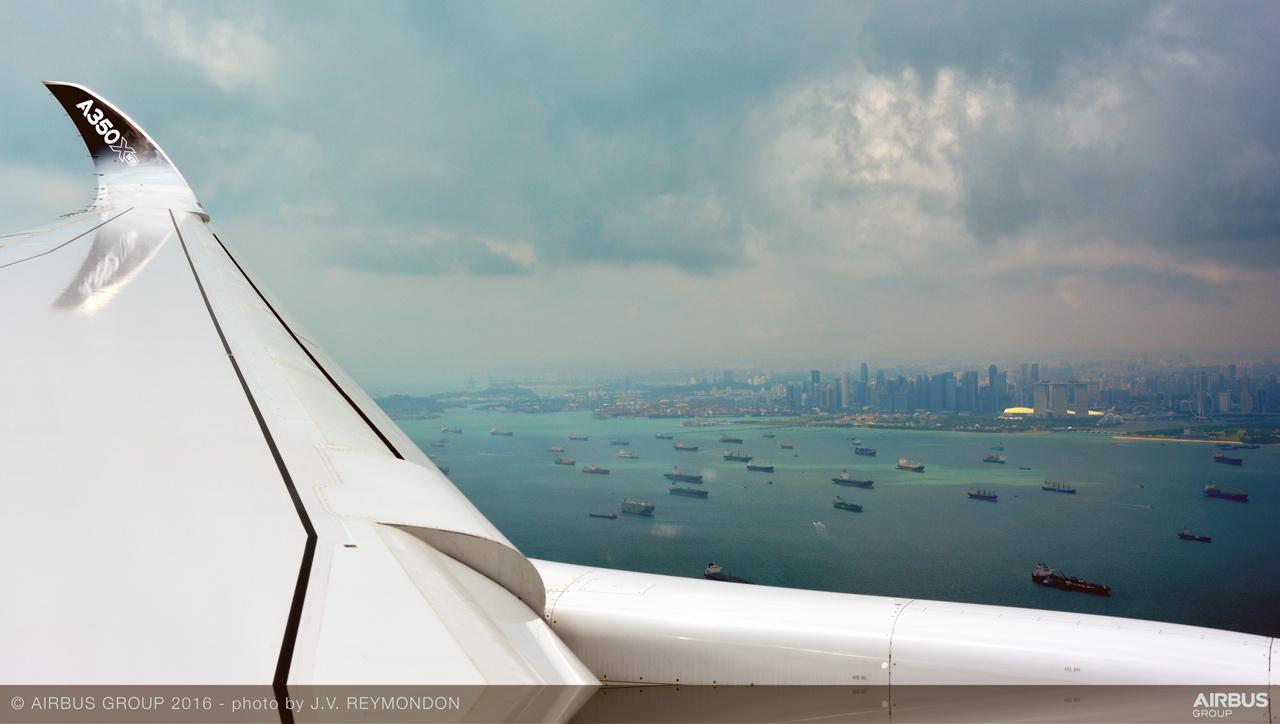
– A saját munkájának fókusza azonban ennél konkrétabb, ugye?
– Igen, én főként az okos gyártás és a fejlett robotika területeivel foglalkozom. Egy új „okos műhely” kialakításán dolgozunk, amelyben intelligens, hálózatba kapcsolt eszközök karcsúsítják a folyamatokat és biztosítják a hibamentes folyamatokat a műhelyek számára.
– Tudna mondani egy konkrét példát?
– Természetesen. Gondoljon arra a több százezer lépésből álló folyamatra, amelyet el kell végezni egy repülőgép összeszereléséhez. A folyamat lépéseinek hatalmas száma miatt nem lehet minden egyes lépéshez külön feladatot meghatározni a munkaállomások szintjén. Ehelyett a folyamat lépéseit összefogva, teljes folyamatként kell menedzselni. A legtöbb összeszerelési műveletben szerepel fúrási művelet, egy ellenőrzési művelet (például mérés) és egy csavarmeghúzási művelet. E folyamatok több lépése is történhet egyetlen munkaállomáson, ám akár több munkaállomásra vagy összeszerelő sorra szétosztva is történhetnek, sőt adott esetben különböző gépkezelők megosztott hatáskörébe is tartozhatnak. Például különböző nyomatékkal és szögben kell meghúzni ugyanazt az elemet a meghúzási folyamat különböző szakaszaiban ugyanazon a fizikai helyen. Éppen ezért, ha valami hiba történik az egyik ilyen folyamat során, akkor az költséges és célzott javítást igényel, hiszen az alkatrész nem a megfelelő munkaállomáson található az üzemben. Így hatalmas potenciál rejlik e folyamatok jobbítására a kéziszerszámok intelligensebbé tétele által, a hálózatba kapcsolásukkal például dinamikusan az adott feladathoz állíthatók be a szerszámok.
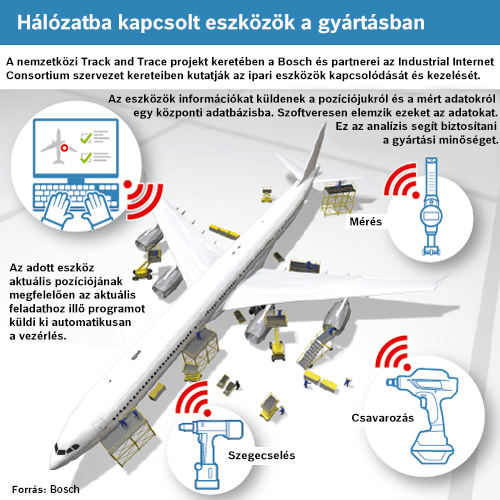
– Milyen eszköztípusokat vesznek számításba?
– Most éppen az okosabb kézi fúrókra, csavarbehajtókra és mérőeszközökre koncentrálunk. Két eltérő rendszert próbálunk ki: vagy magában az eszközben található az intelligens képességeket biztosító modul vagy a kezelők viselik a ruhájukon, például egy öv formájában. Később a robotok és a CNC-gépek integrációját is megvizsgáljuk majd ugyanilyen rendszerfelépítés mentén.
– Hogyan fest a megoldásuk?
– Minden egy platformhoz kapcsolódik, amely összeköti a speciális hardvert és szoftvert. Egy olyan rendszerfelépítést használunk, amely elosztott intelligenciához csatlakozik, ennek elemei a folyamataink minden eszközében megtalálhatók. Elsőként ott vannak az intelligens eszközök. A jövő gyárában használt kéziszerszámok vagy saját fedélzeti szabályzóegységgel rendelkeznek majd vagy kompatibilisek lesznek a viselhető vezérlőegységekkel. Ez fontos a folyamatok bemeneti adatainak helyi feldolgozásához, az eszköz fizikai használatához kapcsolódó fedélzeti érzékelőkkel és szabályzókkal együttműködve. Természetesen ennek kapcsán a lehető legnagyobb mértékben kihasználják a vezeték nélküli kapcsolódás nyújtotta lehetőségeket.
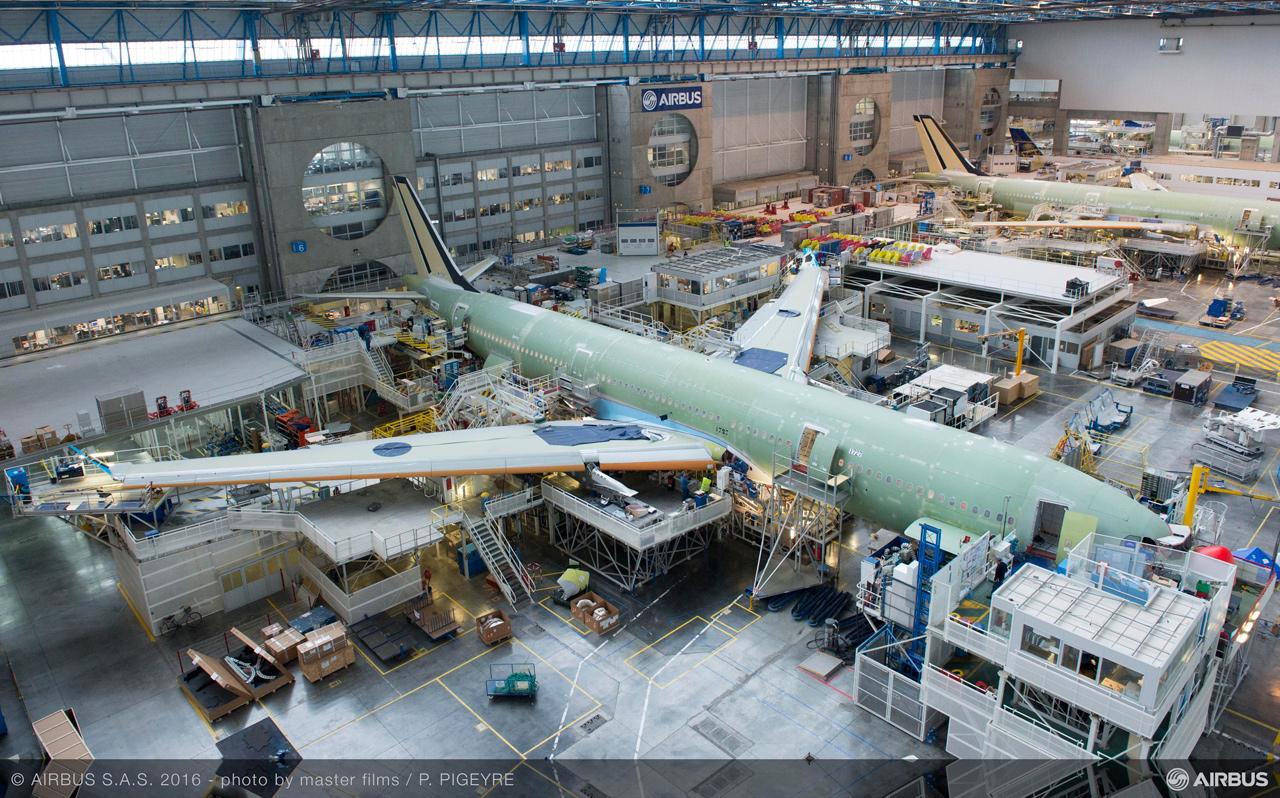
– Mi a helyzet az eszközök integrációjával?
– A múltban tradicionális, központosított megközelítést alkalmaztunk, azonban ez nem elég hatékony a heterogén rendszerek valós idejű menedzseléséhez a kisebb infrastruktúraköltségek igényét is figyelembe véve. Éppen ezért most az olyan megoldásokat vizsgáljuk meg alaposabban, amelyek egymással összekötött eszközök együtteseként működnek. Szükséges az adatközlés a rendszerek között vagy a megfelelő szinkronizáció, ám csak olyankor, amikor ezt a helyi vezérlőrendszer kezdeményezi vagy az a teljes folyamat valamely célját szolgálja. Más szóval nem minden eszköz csatlakozik folyamatosan a központi háttérrendszerhez. Ám az eszközök képesek kapcsolódni egymáshoz, információt és utasításokat cserélni. Ez sok problémát megold – például azt, amikor a repülőgép belsejében dolgozva nem elérhető a vezeték nélküli hálózat.
– Hogyan követik az eszközöket és miként kapcsolják az eszközök információit a termelési adatokhoz?
– A beltéri lokalizáció fontos, akárcsak a MES (gyártásvégrehajtó rendszer) és PLM (termékéletciklus-menedzsment) rendszerek adataival való integráció. A szerszámok és munkadarabok lokációs adatainak automatikus egyeztetése a PLM-adatokkal szintén fontos. Az egyeztetést különböző pontossági adatok (lásd ISO 15725) alapján és az alkalmazás függvényében kezdeményezik. Egy eszköz lokalizációja az összeszerelő csarnokban vagy a munkaállomáson belül nem ugyanaz a feladat, mint egy kéziszerszám csúcsát követni egy önálló munkadarabon végzett folyamat különböző lépései során. Az első esetben a követési adatok pontatlansága több tíz centiméter vagy akár több méter is lehet, míg a második esetben már pár tized milliméter is pontatlanságot jelent. A rendszerintegrációnak figyelembe kell vennie a kontextusfüggő, adaptív viselkedéseket annak érdekében, hogy elkerülje a hibákat és a nem megfelelő minőségű eredményeket.
– Vagyis a lokalizációs adatokat a háromdimenziós termékéletciklus-menedzsment adatokkal integrálják?
– Nem egészen. Tapasztalatból tudjuk, hogy a közvetlenül a mérnököktől érkező CAD/CAM (számítógéppel segített tervezés, illetve számítógéppel segített gyártás) modellek néha túlságosan részletesek és aprólékosak a mi céljainkra. Éppen ezért most egy olyan új, köztes rétegen dolgozunk, amely egyszerűsített XML adatkészletet használ a pozicionáláshoz. Ez a réteg segít integrálni a kéziszerszámokat a háromdimenziós termékéletciklus-menedzsment réteggel. Az is fontos szempont, hogy nem építhetünk arra, hogy az összeszerelést végző munkatársak majd egy teljes háromdimenziós modellező környezetben konfigurálják a munkakörnyezetüket. Emiatt egy egyszerűbb konfigurációs alkalmazást is építenünk kell.
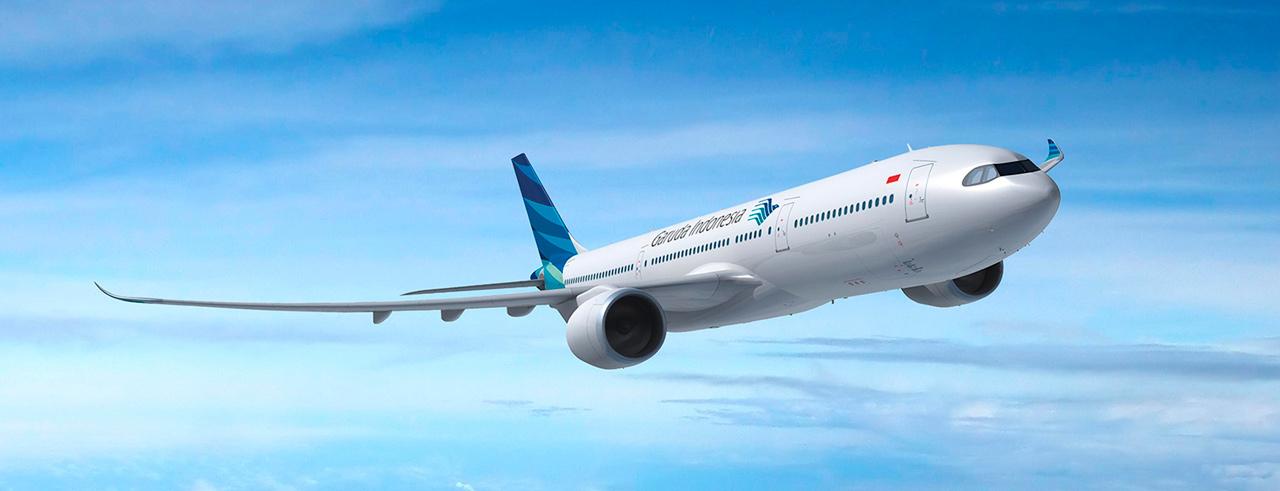
– Úgy hangzik, hogy sok különböző termelési berendezésnek és IT-rendszernek kell kommunikálnia és együttműködnie egymással. Hogyan vezetnek be egy ilyen megoldást egy igencsak heterogén, sok különböző beszállítót érintő környezetben?
– Az elterjesztés fontos kérdéskör, valamint a nyílt interfészekre és az interfészalapú integrációra irányuló egyértelmű fókusz. Legfőképpen az alkalmazásprogramozási interfész (API) jelentette szoftveres nyitottság teszi lehetővé a hatékony integrációt. Éppen ezért robusztus szabványokon alapuló semleges interfészeket határozunk meg, így a mérnökeink, valamint a beszállítóink és partnereink is kifejleszthetnek olyan eszközöket és alkalmazásokat, amelyek illeszkednek az összeszerelést támogató rendszerünkbe. A nagyarányú heterogenitás miatt ez a fajta integratív megközelítés az alapja a jövőbeli termelési rendszerünknek.
Dirk Slama
Ez a szöveg a Dirk Slama, Frank Puhlmann, Jim Morrish és Rishi M Bhatnagar által jegyzett Enterprise IoT című könyv (O’Reilly kiadó, 2015) kivonata. Dirk Salama a Bosch Software Innovations üzletfejlesztési igazgatója.