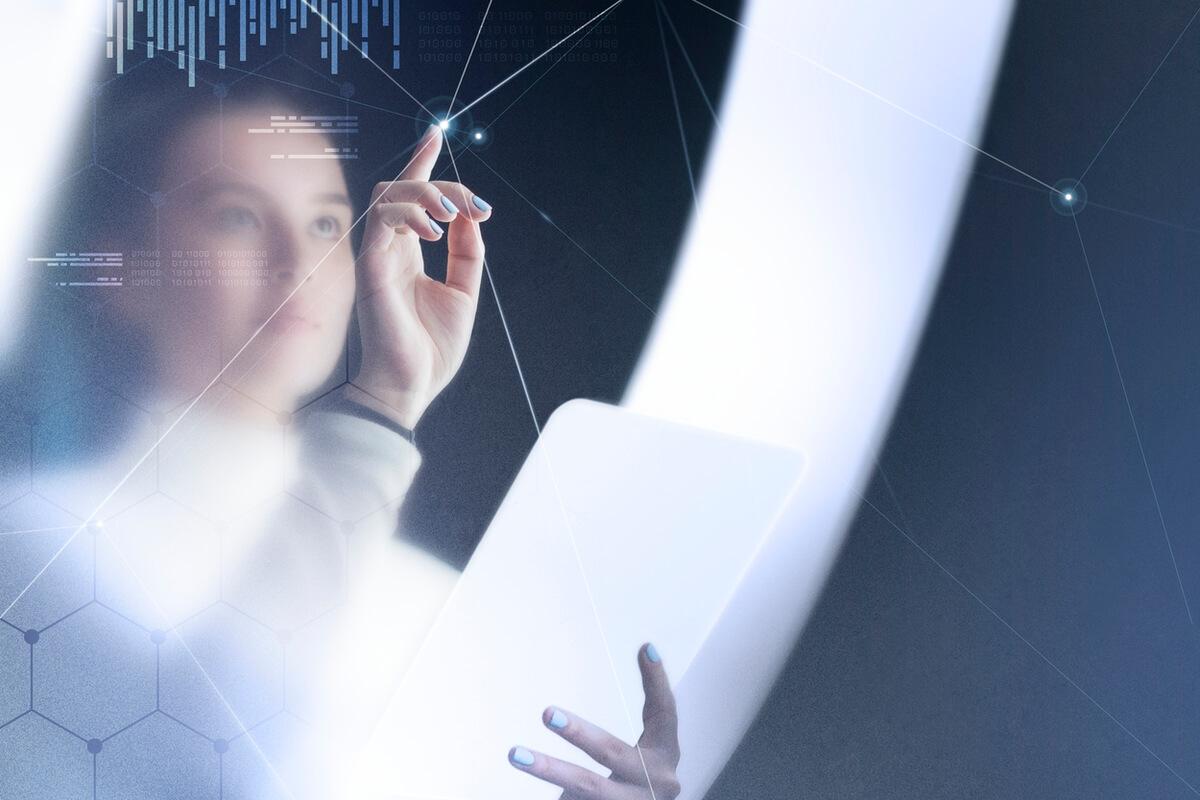
A digitalizáció, a hálózatba kapcsoltság és a mesterséges intelligencia megváltoztatja a munkamódszereket. Nemcsak az irodában, hanem a gyártásban is új folyamatok jönnek létre, amelyek jelentősen meghatározzák a „Jövő Gyárát”. A hálózatba kapcsolt gépekkel és berendezésekkel nagyobb termelékenység érhető el. Ráadásul az erőforrások és az energia hatékonyabb felhasználásával még a környezetet is védjük. Ezek az intelligens eszközök folyamatosan tájékoztatják a hálózatba kapcsolt munkavállalókat, sőt akár fel is készítik őket az új feladatokra.
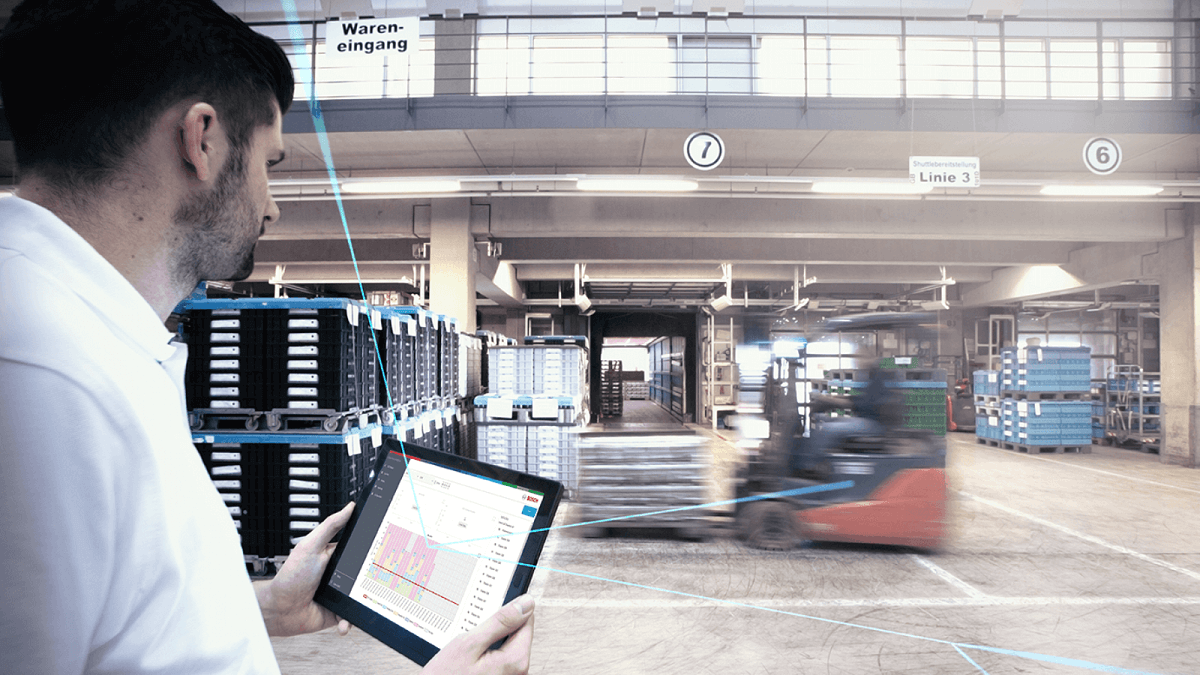
Intelligens IIoT-segítők
A Bosch jihlavai (Csehország) gyárában egy 12 méter hosszú autonóm szállítórobot juttatja el az üres ládákat a termelésbe, majd a nap végén a dízelszivattyúkkal teli dobozokat viszi vissza a raktárba. Ezt a feladatot korábban kizárólag emberi munkaerővel oldották meg. A jelenlegi folyamatban, amikor a jármű megérkezik, a gyártásban dolgozó munkatárs kézi üzemmódra vált, majd néhány métert maga vezeti a robotot: megállítja és kirakja a ládákat, majd újakat rak be. Aztán megnyomja a kijelzőt és az önvezető robot máris a raktár felé veszi az irányt, így a nap végére több kilométer vezetéstől kíméli meg a dolgozókat.
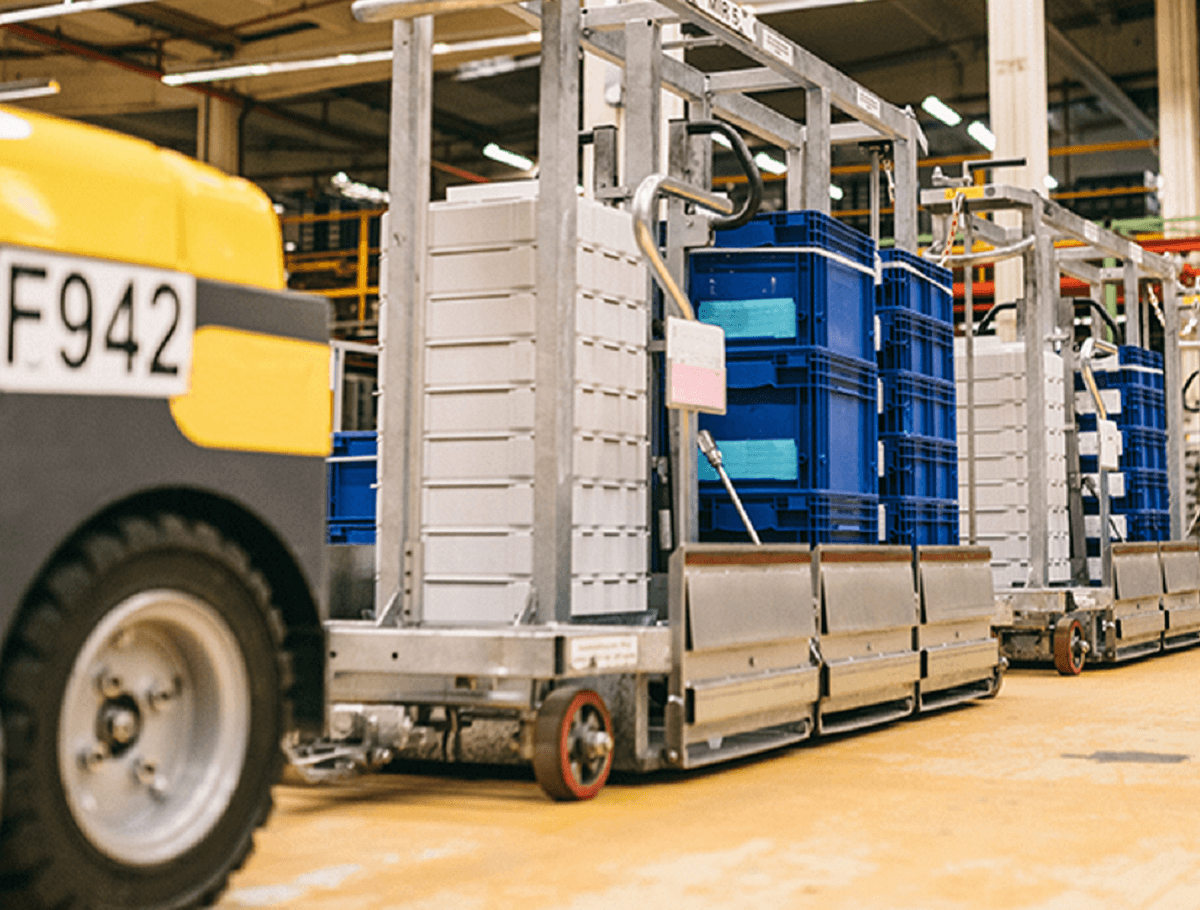
Másik hasonló megoldás a Bosch Rexroth ActiveShuttle vezető nélküli szállítórendszere, amely a kis teherhordókkal (SLC) megrakott görgős kocsikat autonóm módon és gyorsan mozgatja A-ból B-be, például az áruraktárból közvetlenül a felhasználási helyre. Így a logisztikai folyamatok optimalizálhatók, a hely- és az anyagigény csökkenthető, az átfutási idők pedig lerövidíthetők. Intuitív és könnyen kezelhető, biztonságosan használható az emberek környezetében is.
Nincs több papírmunka
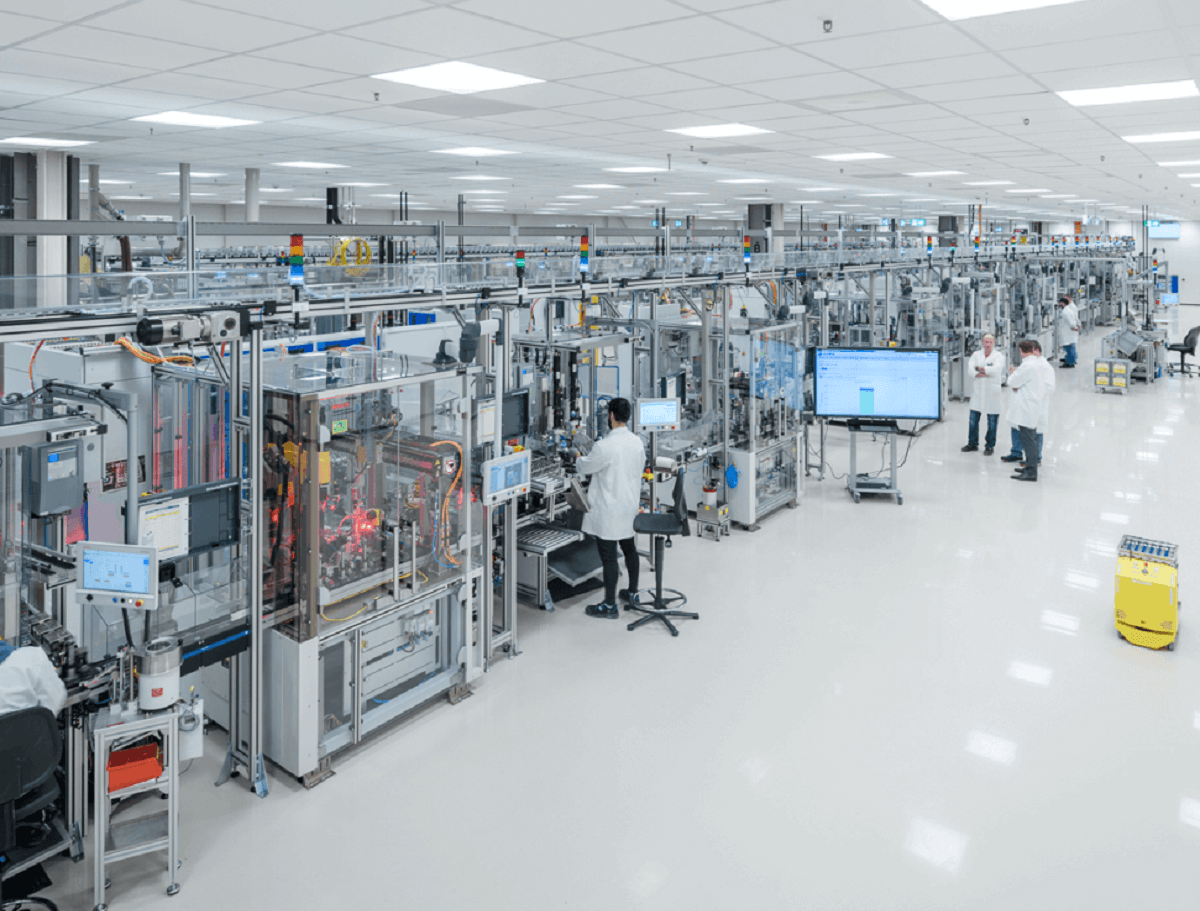
A Nexeed MES szoftvernek köszönhetően minden adat könnyen hozzáférhető a Bosch reutlingeni (Németország) gyárában. Ez a termelésirányítási rendszer képes az összetett gyártósorok vezérlésére, valamint megkönnyíti a termelés és a kiszolgálás közötti kommunikációt is. A hibákat automatikusan a gyártósor digitális műszaknaplójába rögzíti, ráadásul a gépkezelők további részleteket, adatokat adhatnak hozzá, vagy karbantartó szakértő segítségét kérhetik, ami korábban sok papírmunkával járt. A hibák és elakadások akár több hónapra visszamenőleg okostelefonon is nyomon követhetők, valamint az is, hogy egy adott hiba milyen gyakran fordul elő. Amennyiben a javításhoz alkatrészre van szükség, azonnal ellenőrizhető, van-e raktáron.
”Fejlesztjük és alkalmazzuk, teszteljük az új Ipar 4.0 megoldásainkat a saját gyárainkban, aminek számos előnye van. Egyrészről a valós, működés közben keletkező tapasztalatainkat be tudjuk építeni a termékekbe, másrészt gyártóközegből származó referenciákkal tudunk szolgálni partnereinknek. Ez az a kettősség, amivel a piacon egyedülállók vagyunk.
Ács István – ügyvezető igazgató, Bosch Rexroth Kft.
A Jövő Gyárában robotok és algoritmusok kezelik a rutinfeladatokat, az emberek és a gépek szorosabban együttműködnek, a digitális megoldások pedig átszövik a munka és a gyártás összes területét. A cél a hatékonyság növelése, a minőség javítása, a fizikai munka mennyiségének csökkentése, mindemellett több idő jut az értékteremtő feladatokra.
Sőt, mindez még az éghajlatot is védi. A hatékonyság növelése az erőforrások jobb beosztásával és az energia hatékonyabb felhasználásával is jár, ez pedig már önmagában jótékony hatással van a környezetre. A Bosch azonban ennél is tovább megy. A Nexeed Ipar 4.0. szoftverrel ellátott, saját Energy Platform programja segítségével könnyebbé teszi az energiafogyasztás mértékének előrejelzését, egyenletessé teszi a rendszer energiaterhelését, valamint jelzi és kijavítja az egyes gépek energiafogyasztási eltéréseit. A platformot mára több mint 120 telephelyen és több mint 80 ügyfélprojektben használják. A Bosch Rexroth egyik, Ipar 4.0 terén élenjáró üzemében, a németországi Homburgban ezzel a szoftverrel gyártott termékenként több mint 40 százalékkal sikerült csökkenteni az energiaigényt.
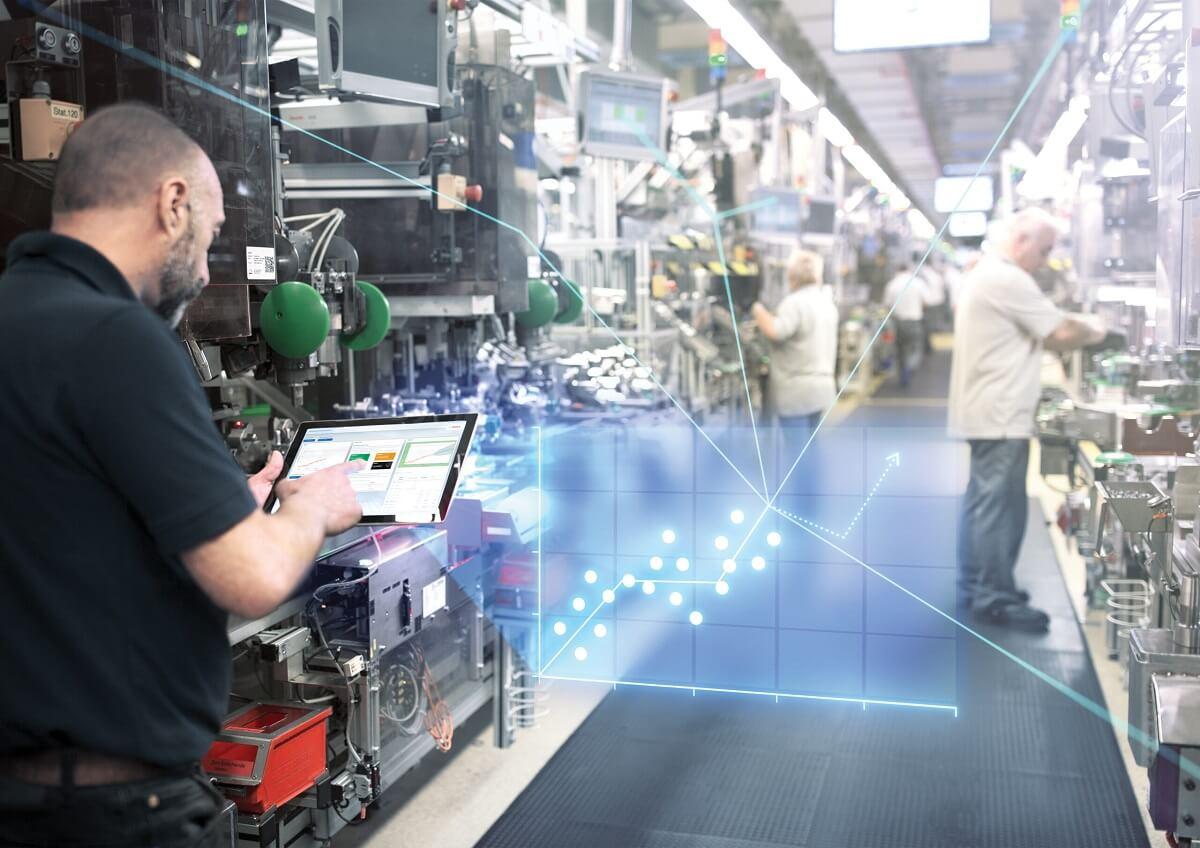